The battery manufacturing industry stands at a critical juncture where precision and quality control determine market leadership. With global demand for lithium-ion, lead-acid, and nickel-cadmium batteries surging, manufacturers face mounting pressure to enhance production efficiency while maintaining impeccable quality standards. Traditional inspection methods are proving inadequate in meeting these evolving demands, particularly as battery technologies become more sophisticated and compact.
Recent advancements in imaging technology are revolutionizing how batteries are manufactured, inspected, and validated. These innovations address critical challenges in production, from material uniformity to final assembly verification, ensuring unprecedented levels of quality control. Among these breakthrough technologies, Time-of-Flight (ToF) camera systems have emerged as a game-changing solution, offering real-time, three-dimensional inspection capabilities that are transforming the manufacturing landscape.
Leopard Imaging’s ToF Technology Leading the Manufacturing Revolution
Leopard Imaging’s ToF camera technology represents a quantum leap in manufacturing inspection systems. This sophisticated imaging solution, which builds upon traditional ToF camera designs with proprietary enhancements, utilizes advanced photonic sensors that measure the time taken for light to bounce off objects and return to the sensor, creating precise three-dimensional maps of battery components with submillimeter accuracy. The system’s integration of Active Alignment (AA) technology ensures optimal sensor positioning, delivering consistent, high-precision measurements across the entire production line.
Where AI Meets Manufacturing Excellence
The true power of Leopard Imaging’s ToF system lies in its seamless integration of artificial intelligence. Advanced algorithms process the captured 3D data in real-time, enabling instantaneous detection of defects and deviations from manufacturing specifications. This AI-driven approach allows for continuous monitoring of production parameters, ensuring that every battery component meets stringent quality standards before proceeding to the next manufacturing stage.
Transforming Battery Production Through Advanced Implementation
The implementation of ToF technology in battery manufacturing represents a paradigm shift in quality control processes. Unlike conventional inspection methods, ToF cameras provide comprehensive, three-dimensional analysis of battery components during production. This capability enables manufacturers to detect subtle variations in electrode coating thickness, identify microscopic defects in cell assembly, and ensure precise alignment of battery components – all in real-time.
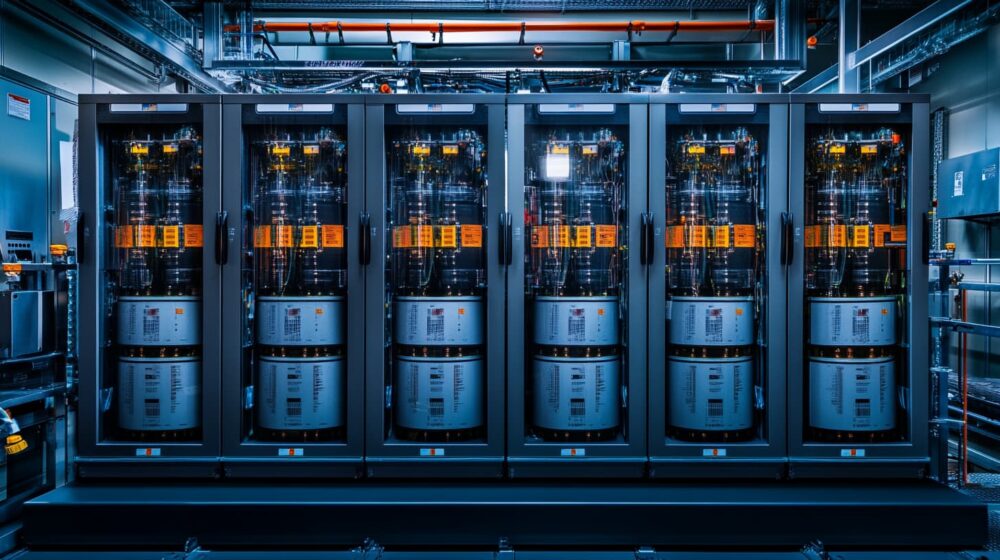
Recent production data indicates that facilities utilizing ToF camera systems have experienced up to a 40% reduction in defect rates and a 25% increase in production throughput. These improvements stem from the technology’s ability to identify and address potential issues before they impact downstream processes.
From Integration to Operation
The deployment of ToF camera systems follows a structured implementation process, typically spanning 8-12 weeks from initial installation to full operation. Manufacturing line integration requires minimal modification to existing production systems, with most installations completed during planned maintenance windows. Staff training programs, typically conducted over a two-week period, ensure operators and maintenance personnel can effectively manage and maintain the system.
Initial system costs typically range from $50,000 to $150,000 per production line, depending on the complexity of implementation. However, manufacturers report average payback periods of 12-18 months through reduced waste, improved yield, and decreased quality control staffing needs. Annual maintenance costs average 5-7% of the initial investment, significantly lower than traditional inspection systems.
Beyond Traditional Imaging: A Comparative Perspective
Traditional imaging solutions, while valuable, fall short in several critical areas when compared to ToF technology. Two-dimensional optical systems struggle with depth perception and cannot effectively measure component thickness or detect subtle surface variations. X-ray systems, though powerful, are costly to implement and maintain, requiring specialized safety protocols and facilities.
The following comparison illustrates the key advantages of ToF technology:
Feature | ToF Camera System | Traditional Optical | X-ray Imaging |
3D Capability | Real-time 3D mapping | Limited/None | Partial |
Speed | Millisecond response | Moderate | Slow |
Integration Ease | High | Moderate | Complex |
Maintenance Cost | Low | Moderate | High |
AI Integration | Seamless | Limited | Moderate |
Advancing Toward Industry 4.0
The integration of ToF camera systems marks a significant step toward fully automated, intelligent manufacturing processes. These systems generate valuable data that feeds into broader Industry 4.0 initiatives, enabling predictive maintenance, quality trending, and continuous process optimization. Manufacturers implementing these systems report significant improvements in operational efficiency, with some facilities achieving up to 30% reduction in quality-related downtime.
Real-World Implementation
Leading battery manufacturers implementing ToF camera systems have documented remarkable improvements in their production processes. A major electric vehicle battery manufacturer recently reported a 35% decrease in scrap rates and a 28% improvement in first-pass yield after implementing Leopard Imaging’s ToF technology. These results demonstrate the tangible benefits of advanced imaging in modern battery production.
Regulatory Excellence and Safety Standards
ToF camera systems comply with essential manufacturing and safety standards, including:
- IEC 61496-1/-2 for electrical safety
- ISO 13849-1 for functional safety
- IP65/67 ratings for industrial environment protection
The technology meets FDA 21 CFR Part 11 compliance requirements for electronic systems in manufacturing, ensuring data integrity and traceability. Regular calibration and validation procedures maintain system accuracy and reliability, meeting stringent quality management standards such as ISO 9001:2015.
Embracing the Future of Battery Manufacturing
The integration of cutting-edge imaging technology, particularly ToF camera systems, represents a crucial step forward in battery manufacturing excellence. The combination of precise 3D imaging, AI-driven analysis, and real-time monitoring capabilities provides manufacturers with unprecedented control over their production processes. As the industry continues to evolve, those who embrace these advanced technologies will be best positioned to meet growing demand while maintaining the highest quality standards.
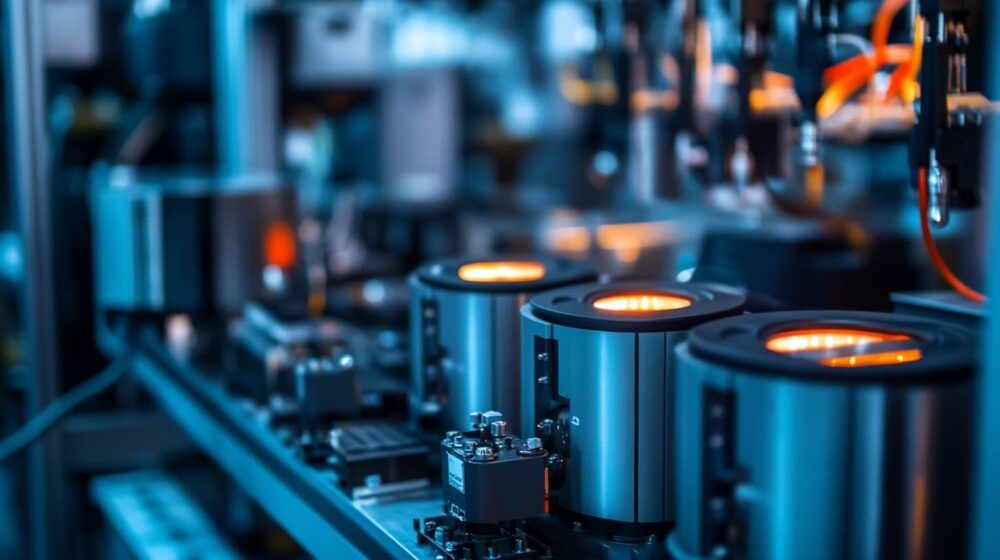
For manufacturers looking to enhance their production capabilities, the implementation of ToF camera technology offers a clear path forward. The documented improvements in quality, efficiency, and cost reduction make a compelling case for investment in these advanced imaging solutions. As battery technology continues to advance, the role of sophisticated imaging systems in ensuring manufacturing excellence will only grow in importance.